Work centers¶
Work centers are where Manufacturing work orders are processed, and can be used to track costs, make schedules, plan capacity, organize equipment, and track efficiency. Specifying a work center is required when a work order is defined in the Operations tab of a bill of materials (BoM) for a product.
Important
Work centers only appear if the Work Orders setting is enabled. To do so, navigate to , then tick the Work Orders checkbox. Work orders can be managed in the Manufacturing app by selecting .
See also
Work center configuration¶
Create a new work center¶
In the Manufacturing app, select New button to open a new work center form.
and click the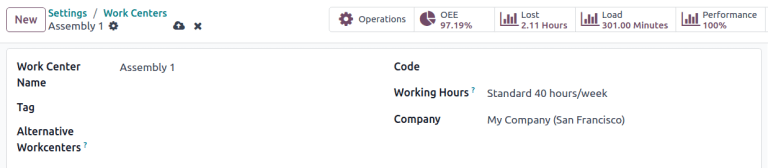
Work Center Name: the label for the work center used to select it on a work order or on the reporting dashboards
Tag: reusable labels that can be used to sort work centers in list view
Alternative Workcenters: where a work order should be carried out if this work center is not available
Code: reference id for the work center that is displayed in the list view
Working Hours: the hours that work center can be used during the week
Working hours¶
Working hours define when a work center should operate, based on a one- or two-week schedule. These hours also form the basis for calculating overall equipment efficiency (OEE).
Note
By default, Odoo uses the Standard 40 hours/week
working hours, which expects work centers to
operate between 8:00 AM and 5:00 PM on Monday through Friday.
To change the working hours, hover over the current Working Hours value and click the (Internal link) icon to open the working hours form.
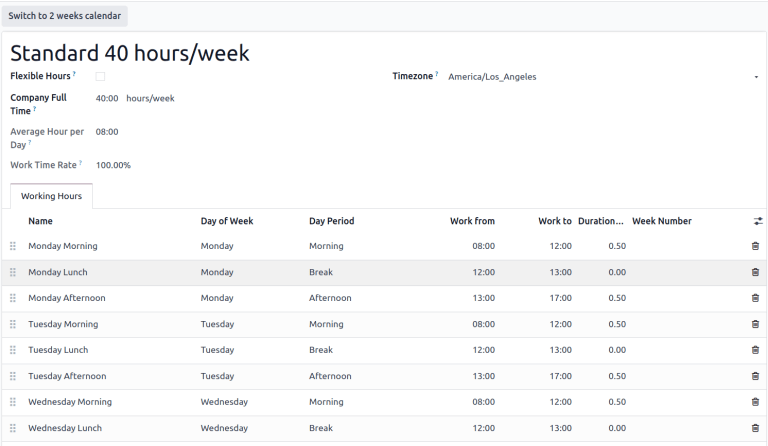
To create a new set of working hours, click the New button and give it a name. From here, edit any Work from or Work to value to adjust the time range. Remove a line by clicking click the (trash) icon. To create a new time range, click Add a line at the bottom of the list.
Set productivity standards and allowed employees¶
The General Information tab on the work center form allows for productivity goals to be assigned to a work center. These are used as the basis for calculating how much of the potential time the work center is being used and its operating costs.
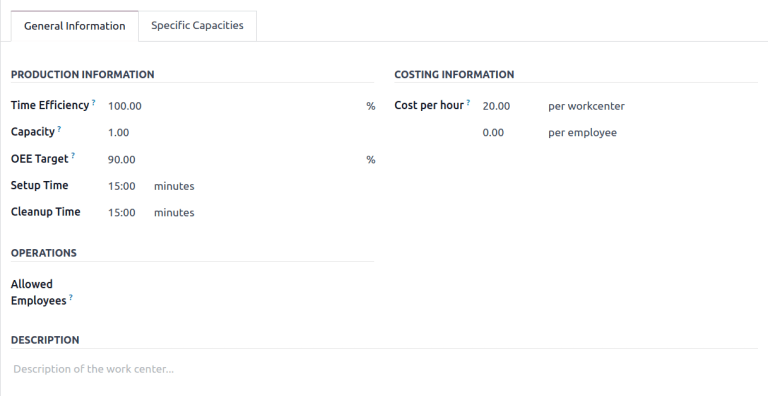
Time Efficiency: a multiplier for how using this work center affects the normal speed of execution of a work order
Example
If a work center has older equipment and work orders take twice as long to produce, the
Time Efficiency
would be50.00%
.Capacity: the number of products that can be processed at the work center simultaneously
OEE Target: the target for efficiency at the work center
Example
If a work center is available for
8 hours per day
but is only expected to be used for7 hours per day
, the OEE would be87.50%
. \(7/8*100=87.5\)See also
Setup Time: the time required before work can commence on a work order
Cleanup Time: breakdown or cleanup time required after a work order is finished
Cost per hour: the operating expense of that workstation. The per employee value is for estimating the average cost per employee.
See also
Allowed Employees: the employees who can perform work at the work center. If blank, all employees are allowed.
Example
If equipment at a work center requires a certification to operate, Allowed Employees could list only those employees who have the certification.
Set production capacities¶
The Capacity setting on a work center creates a default value for how many units can be produced at one time in a work center. To specify that a work center can produce different quantities of different products, select the Specific Capacities tab.
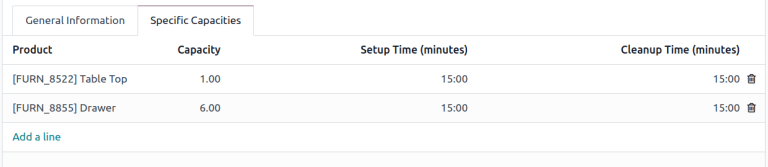
Tip
To specify production capacities in different measurements from a count of units, enable the Units of Measure feature in the Inventory app.
See also
Integrate IoT devices¶
The IoT Triggers tab enables the integration of IoT devices with a work center:
Device: specifies the IoT device to be triggered
Key: the security key for the device
Action: the IoT device action triggered
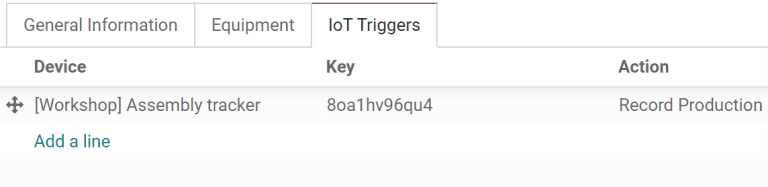
Assigning equipment to work centers¶
The Maintenance app makes it possible to add specific equipment to a work center and individually track its costs and productivity. It also adds the Equipment and Maintenance tabs to the work center form, used to list equipment and schedule maintenance activities.
See also
Configure equipment¶
Using the Equipment tab, it is possible for specific pieces of equipment to be assigned to a work center. The following information is displayed for each piece of equipment added:
Equipment Name: the name of the piece of equipment
Technician: the technician responsible for servicing the equipment
Equipment Category: the category the equipment belongs to
MTBF: mean time between failures; the average time that the piece of equipment will operate before failing
MTTR: mean time to recovery; the average time it takes for the equipment to become fully operational again
Est. Next Failure: an estimate of when the next equipment failure will occur
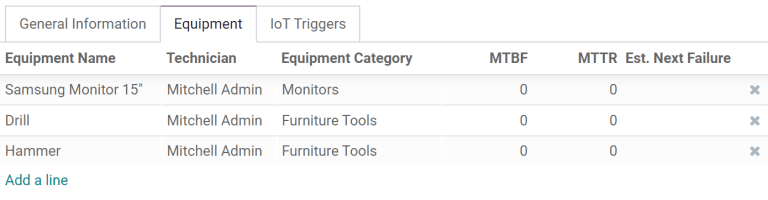
Note
MTBF, MTTR, and Est. Next Failure are all calculated automatically based on past failure data, if any exists.
Work center planning¶
The currently scheduled work orders can be viewed by accessing
.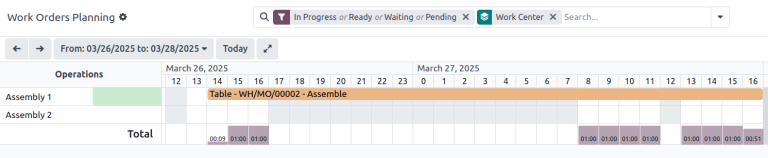
Different views show how many individual work orders are scheduled, how many minutes of each hour the work center is in production, and the dates and times that are currently scheduled for work orders. Times and planned work centers can be changed by clicking to access the individual work order.
Work center performance¶
Performance for an individual work center can be viewed by selecting
, and clicking on a work center. Metrics are displayed in smart buttons at the top of the form.
OEE: overall equipment effectiveness, the percentage of time that the work center has been productive out of its available work hours.
See also
Lost: the amount of time lost due to work stoppages
Load: the amount of time it will take to complete the current workload
Performance: the real duration of work time, shown as a percentage of the expected duration
Use case: measuring performance by shift using work centers¶
Work centers support defined working hours, enabling the tracking of production efficiency by shift. To configure shift-based tracking, create working hours for each of the shifts, then duplicate versions of each work center for each of the shifts. With this setup, comparing shift productivity can be done with any of the available reporting tools.
Working hours for multiple shifts¶
To create working hours for multiple shifts, open a work center form and in the Working Hours field click the (Internal link), and then click the New button to create a new set of hours for the second shift.
Example
A manufacturer has two shifts: a day shift from 5 AM to 1 PM and a night shift from 1 PM to 9 PM. Starting from any existing work center, edit the existing working hours to match the day shift.
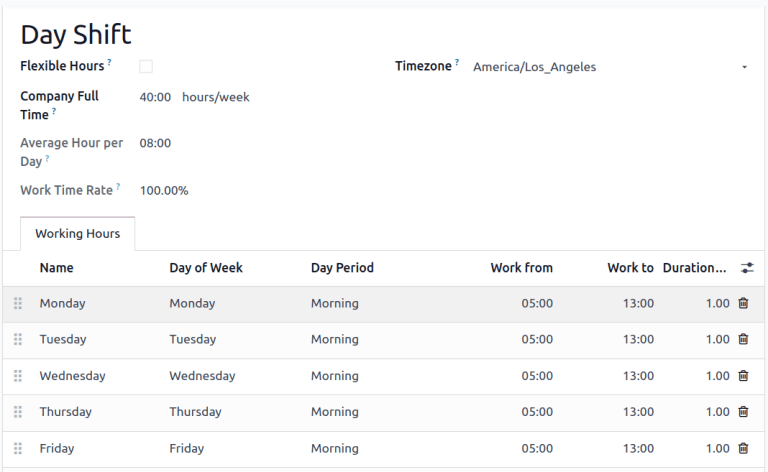
Once the day shift is saved, click the (cog) icon and select
Duplicate. Rename this new schedule Night Shift
and change each Work
from to 1 PM and Work from to 9 PM.
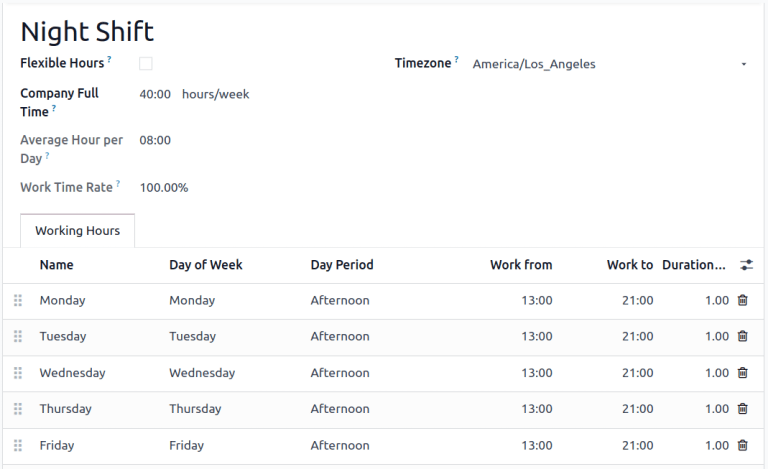
Work centers for multiple shifts¶
To create the duplicate work centers, return to the work center view by navigating to
and duplicating each of the work centers that are used by both shifts, either on the individual work center forms, or directly from the list view.Tip
To duplicate work centers directly from the list view, click the (checkbox) that appears above the list items to select all. Then, click the Actions button at the top of the list and select Duplicate.
Example
A manufacturer has two work centers,
Assembly Line 1
andAssembly Line 2
, and two working hours,Day Shift
andNight Shift
.![]()
To create versions of Assembly Line 1
and Assembly Line 2
for each shift, duplicate each of
the work centers. Select the first work center and add the shift name in that work center’s name
and assign it the appropriate working hours. Optionally, configure each work center to use its
opposite shift counterpart as an alternate work center to make sure that manufacturing orders get
assigned to both. Tags can also help make a visual distinction between each shift.
Tip
Use the (left arrow) and (right arrow) buttons in the top left corner to move on to the next form in the list without returning to the list view.
Reports comparing different shifts¶
With multiple work centers created to represent shifts, reports that sort by work center will now compare shifts. This can be used to compare the number of work orders that are being assigned each shift, the OEE, or actual time that each shift is taking to produce a product.
Example
A report has been created to compare the time efficiency of two shifts producing the same product in the same work center.
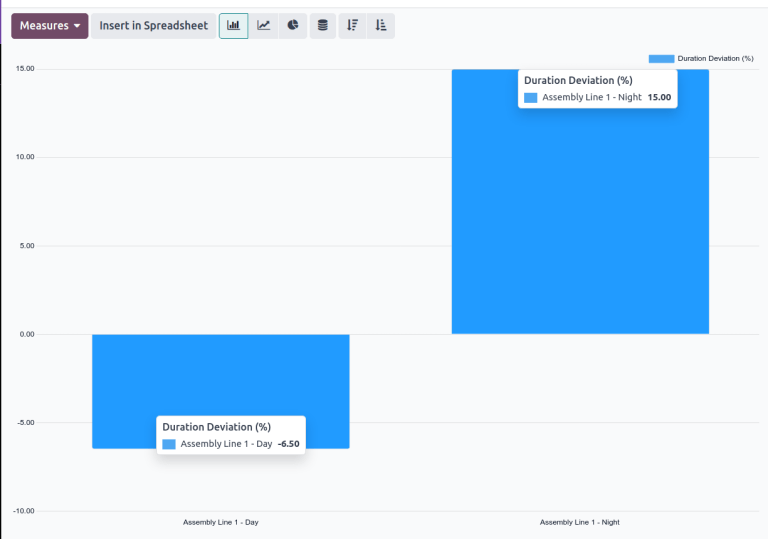
To create this report, go to Remove icon on its right side. Next, click the Measures button and select Duration Deviation (%)
and click to remove the Ready or Waiting or Pending or In Progress filter by clicking theIn this case, the day shift has on average taken more than the expected time to produce products (-6.50%) while the night shift took less than the expected time (15.00%).